Most corrosion of metal materials occurs in atmospheric environment, because the atmosphere contains corrosive components such as oxygen and pollutants, as well as corrosion factors such as humidity and temperature changes. Salt spray corrosion is one of the most common and destructive atmospheric corrosion.
Principle of salt spray corrosion
The corrosion of metal materials by salt spray is mainly caused by the infiltration of conductive salt solution into the metal and the electrochemical reaction, forming the micro-battery system of “low potential metal – electrolyte solution – high potential impurity”. Electron transfer occurs, and the metal as the anode dissolves and forms a new compound, namely the corrosion. Chloride ion plays a major role in the corrosion damage process of salt spray, which has a strong penetrating power, easy to penetrate the metal oxide layer into the metal, destroy the blunt state of the metal; At the same time, chloride ion has a very small hydration energy, which is easy to be adsorbed on the surface of the metal, replacing the oxygen in the oxide layer protecting the metal, so that the metal is damaged.
Salt spray corrosion test methods and classification
Salt spray test is an accelerated corrosion resistance evaluation method for artificial atmosphere. It is a concentration of brine atomized; Then spray in a closed thermostatic box, by observing the change of the tested sample placed in the box for a period of time to reflect the corrosion resistance of the tested sample, it is an accelerated test method, the salt concentration of chloride salt spray environment, but the general natural environment salt spray content several times or dozens of times, so that the corrosion rate is greatly improved, salt spray test on the product, The time to get results has also been drastically reduced.
Salt spray test before and after
The corrosion time of a product sample may take a year or even several years when tested in natural environment, but similar results can be obtained in days or even hours when tested in artificial simulated salt spray environment.
Salt spray tests are mainly divided into four types:
① Neutral salt spray test (NSS)
② Acetic acid spray test (AASS)
③ Copper accelerated acetic acid spray test (CASS)
(4) Alternating salt spray test
Salt spray corrosion testing equipment
Evaluation of salt spray test results
The evaluation methods of salt spray test include rating method, corrosion occurrence evaluation method and weighing method.
01
Rating method
The rating method divides the percentage of the corrosion area to the total area into several grades according to a certain method, and takes a certain grade as the basis for qualified judgment. This method is suitable for the evaluation of flat plate samples. For example, GB/T 6461-2002, ISO 10289-2001, ASTM B537-70(2013), ASTM D1654-2005 all use this method to evaluate salt spray test results.
Protection rating and appearance rating
RP and RA values are calculated as follows:
Where: RP is the protection rating value; RA is the appearance rating value; A is the percentage of the corroded part of the matrix metal in the total area when RP is calculated; RA is the percentage of the corroded part of the protective layer in the total area.
Overlay classification and subjective evaluation
The protection rating is expressed as: RA/ -
For example, when slight rust exceeds 1% of the surface and is less than 2.5% of the surface, it is expressed as: 5/ -
Appearance rating is expressed as: – /RA value + subjective evaluation + overlay failure level
For example, if the spot area is more than 20%, it is: – /2mA
The performance rating is expressed as RA value + subjective evaluation + overlay failure level
For example, if there is no matrix metal corrosion in the sample, but there is mild corrosion of anodic covering layer less than 1% of the total area, it is denoted as 10/6sC
A photograph of an overlay with negative polarity towards the substrate metal
02
Method for assessing the presence of corrodes
Corrosion assessment method is a qualitative determination method, it is based on the salt spray corrosion test, whether the product corrosion phenomenon to determine the sample. For example, JB4 159-1999, GJB4.11-1983, GB/T 4288-2003 adopted this method to evaluate the test results of salt spray.
Corrosion characteristic table of common electroplating parts after salt spray test
Calculation method of corrosion rate:
01
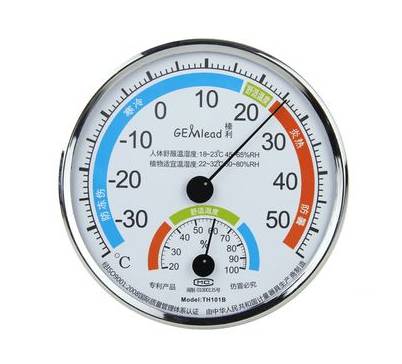
Concentration of solution
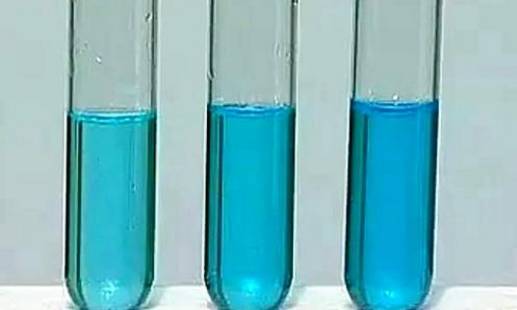
The placement Angle of the sample
The sedimentation direction of the salt spray is close to the vertical direction. When the sample is placed horizontally, its projection area is the largest, and the sample surface bears the most salt spray, so the corrosion is the most serious. The results show that when the steel plate is 45° from the horizontal line, the corrosion weight loss per square meter is 250g, and when the steel plate is parallel to the vertical line, the corrosion weight loss is 140g per square meter. GB/T 2423.17-1993 standard states: “The method of placing the flat sample shall be such that the tested surface shall be at an Angle of 30° from the vertical direction”.
04 PH
lower the pH, the higher the concentration of hydrogen ions in the solution, the more acidic and corrosive. Neutral salt spray test (NSS) pH value is 6.5~7.2. Due to the influence of environmental factors, the pH value of salt solution will change. In order to improve the reproducibility of salt spray test results, the pH value range of salt solution is specified in the standard of salt spray test at home and abroad, and the method of stabilizing the pH value of salt solution during the test is proposed.
05
The amount of salt spray deposition and spray method
The finer the salt spray particles, the larger the surface area they form, the more oxygen they adsorb, and the more corrosive they are. The most obvious disadvantages of the traditional spray methods, including the pneumatic spray method and the spray tower method, are the poor uniformity of the salt spray deposition and the large diameter of the salt spray particles. Different spray methods also have an effect on the pH of the salt solution.
Standards related to salt spray tests.
How long is an hour of salt spray in the natural environment?
Salt spray test is divided into two categories, one is natural environment exposure test, the other is artificial accelerated simulated salt spray environment test.
Artificial simulation of salt spray environment test is to use a test equipment with a certain volume space – salt spray test chamber, in its volume space with artificial methods to create salt spray environment to evaluate the corrosion resistance of the product. Compared with the natural environment, the salt concentration of chloride in the salt spray environment can be several times or dozens of times of the salt spray content in the general natural environment, so that the corrosion speed is greatly improved, and the salt spray test on the product is greatly shortened. For example, it may take 1 year for a product sample to be corroded under natural exposure, while similar results can be obtained in 24 hours under artificial simulated salt spray environment.
Artificial simulated salt spray test includes neutral salt spray test, acetate spray test, copper salt accelerated acetate spray test, alternating salt spray test.
(1) Neutral salt spray test (NSS test) is an accelerated corrosion test method with the earliest appearance and the widest application field. It uses 5% sodium chloride brine solution, the solution pH adjusted in the neutral range (6 ~ 7) as the spray solution. The test temperature was set at 35℃, and the settlement rate of salt spray was required to be between 1 ~ 2ml/80cm².h.
(2) acetate spray test (ASS test) is developed on the basis of neutral salt spray test. It is to add some glacial acetic acid to 5% sodium chloride solution, so that the pH value of the solution drops to about 3, the solution becomes acidic, and finally the salt spray is formed from neutral salt spray into acid. The corrosion rate is about three times faster than the NSS test.
(3) Copper salt accelerated acetate spray test (CASS test) is a rapid salt spray corrosion test developed recently abroad. The test temperature is 50℃, and a small amount of copper salt – copper chloride is added into the salt solution to strongly induce corrosion. It corrodes about eight times faster than the NSS test.
Under general environmental conditions, the following time conversion formula can be roughly referred to:
Neutral salt spray test 24h natural environment for 1 year
Acetate mist test 24h natural environment for 3 years
Copper salt accelerated acetate mist test 24h natural environment for 8 years
Therefore, in view of the Marine environment, salt spray, wet and dry alternating, freeze-thaw characteristics, we believe that the corrosion resistance of fishing vessel fittings in such an environment should only be one-third of that of conventional tests.
Therefore, in view of the Marine environment, salt spray, wet and dry alternating, freeze-thaw characteristics, we believe that the corrosion resistance of fishing vessel fittings in such an environment should only be one-third of that of conventional tests.
That’s why we require fishing boats to have Metal halide lamp ballast and capacitors installed indoors. The lamp holder of the 4000w Fishing light on board should be sealed with a material that can withstand more than 230 degrees Celsius. To ensure that fishing lights in the use of the process, will not lose the sealing effect, and into the salt spray, resulting in lamp cap corrosion, resulting in light bulb chip break.
Above, a 4000w fishing lamp that attract tuna was used by a fishing boat for half a year. The captain did not keep the lamp in a dry environment on land or check the seal of the lamp because he was guarding the island for a year. When he used the lamp again after a year, the chip of the lamp exploded
Post time: May-15-2023