Die meisten Korrosion von Metallmaterialien treten in atmosphärischer Umgebung auf, da die Atmosphäre korrosive Komponenten wie Sauerstoff und Schadstoffe sowie Korrosionsfaktoren wie Feuchtigkeit und Temperaturänderungen enthält. Salzspray -Korrosion ist eine der häufigsten und destruktivsten atmosphärischen Korrosion.
Prinzip der Salzspray -Korrosion
Die Korrosion von Metallmaterialien durch Salzspray wird hauptsächlich durch die Infiltration der leitenden Salzlösung in das Metall und die elektrochemische Reaktion verursacht, wodurch das Mikrobatteriesystem von „niedrig potentiellem Metall-Elektrolytlösung-hohe Potentialverunreinigung“ bildet. Der Elektronentransfer tritt auf und das Metall, wenn sich die Anode auflöst und eine neue Verbindung bildet, nämlich die Korrosion. Chloridionen spielt eine wichtige Rolle beim Korrosionsschäden von Salzspray, der eine starke durchdringende Kraft aufweist, die leicht in die Metalloxidschicht in das Metall eindringen kann, den stumpfen Zustand des Metalls zerstören. Gleichzeitig hat Chloridion eine sehr kleine Hydratationsenergie, die leicht an der Oberfläche des Metalls adsorbiert werden kann und den Sauerstoff in der Oxidschicht ersetzt, das das Metall schützt, so dass das Metall beschädigt wird.
Salzspray -Korrosionstestmethoden und Klassifizierung
Der Salzspray -Test ist eine beschleunigte Korrosionsbeständigkeitsbewertungsmethode für die künstliche Atmosphäre. Es ist eine Konzentration von Sole, die atomisiert ist; Sprühen Sie dann in eine geschlossene thermostatische Box, indem Sie die Änderung der getesteten Probe für einen bestimmten Zeitraum beobachten, um die Korrosionsbeständigkeit der getesteten Probe widerzuspiegeln. Aber der allgemeine Salzspray -Gehalt der natürlichen Umgebung mehrmals oder Dutzende Male, sodass die Korrosionsrate stark verbessert wird. Salzspray -Test für das Produkt wurde auch die Zeit, um Ergebnisse zu erzielen, drastisch reduziert.
Salzspray -Test vor und nachher
Die Korrosionszeit einer Produktprobe kann ein Jahr oder sogar mehrere Jahre dauern, wenn sie in der natürlichen Umgebung getestet werden, aber ähnliche Ergebnisse können in Tagen oder sogar Stunden erzielt werden, wenn sie in künstlicher simulierter Salzspray -Umgebung getestet werden.
Salzspray -Tests sind hauptsächlich in vier Arten unterteilt:
① Neutrales Salzspray -Test (NSS)
② Essigsäurespray -Test (Aass)
③ Kupferbeschleunigter Essigsäurespray -Test (Cass)
(4) Wechselsalzspray -Test
Salzspray -Korrosionstestausrüstung
Bewertung von Salzspray -Testergebnissen
Die Bewertungsmethoden des Salzspray -Tests umfassen die Bewertungsmethode, die Bewertungsmethode für Korrosionsaufschlüsse und die Waagemethode.
01
Bewertungsmethode
Die Bewertungsmethode unterteilt den Prozentsatz der Korrosionsfläche in die Gesamtfläche in mehrere Klassen gemäß einer bestimmten Methode und nimmt eine bestimmte Note als Grundlage für ein qualifiziertes Urteilsvermögen. Diese Methode eignet sich zur Bewertung von Flachplattenproben. Beispielsweise verwenden GB/T 6461-2002, ISO 10289-2001, ASTM B537-70 (2013), ASTM D1654-2005 diese Methode, um die Ergebnisse des Salzspray-Testergebnisses zu bewerten.
Schutzbewertung und Erscheinungsbewertung
RP- und RA -Werte werden wie folgt berechnet:
Wo: RP ist der Schutzwert des Schutzes; RA ist der Bewertungswert des Aussehens; A ist der Prozentsatz des korrodierten Teils des Matrixmetalls in der Gesamtfläche, wenn RP berechnet wird. RA ist der Prozentsatz des korrodierten Teils der Schutzschicht in der Gesamtfläche.
Überlagerungsklassifizierung und subjektive Bewertung
Die Schutzbewertung wird ausgedrückt als: ra/ -
Wenn beispielsweise geringfügiger Rost 1% der Oberfläche überschreitet und weniger als 2,5% der Oberfläche beträgt, wird es als: 5/ - ausgedrückt
Die Bewertung der Erscheinung wird ausgedrückt als: - /RA -Wert + subjektive Bewertung + Überlagerungsversagensstufe
Wenn die Spot -Fläche beispielsweise mehr als 20%beträgt, ist es: - /2ma
Die Leistungsbewertung wird als RA -Wert + subjektive Bewertung + Overlay -Ausfallniveau ausgedrückt
Wenn beispielsweise in der Probe keine Matrix -Metall -Korrosion vorliegt, aber eine leichte Korrosion der anodischen Abdeckungsschicht weniger als 1% der Gesamtfläche ist, wird sie als 10/6 SC bezeichnet
Ein Foto einer Überlagerung mit negativer Polarität gegenüber dem Substratmetall
02
Methode zur Bewertung des Vorhandenseins von Korroden
Die Korrosionsbewertungsmethode ist eine qualitative Bestimmungsmethode, die auf dem Salzspray -Korrosionstest basiert, unabhängig davon, ob das Produktkorrosionsphänomen zur Bestimmung der Probe. Zum Beispiel haben JB4 159-1999, GJB4.11-1983, GB/T 4288-2003 diese Methode zur Bewertung der Testergebnisse von Salzspray übernommen.
Korrosion charakteristische Tabelle gemeinsamer Elektroplatten nach Salzspray -Test
Berechnungsmethode der Korrosionsrate:
01
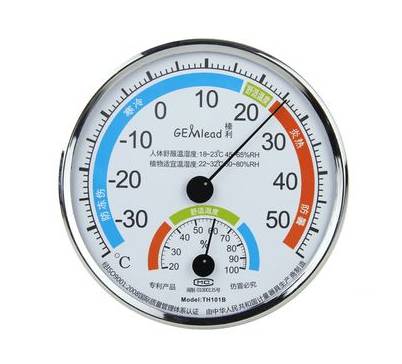
Lösungskonzentration
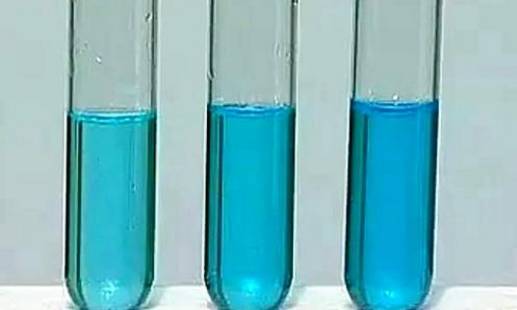
Der Platzierungswinkel der Probe
Die Sedimentationsrichtung des Salzspray liegt nahe an der vertikalen Richtung. Wenn die Probe horizontal platziert wird, ist ihr Projektionsbereich der größte und die Probenoberfläche trägt das meiste Salzspray, sodass die Korrosion am schwerwiegendsten ist. Die Ergebnisse zeigen, dass, wenn die Stahlplatte 45 ° von der horizontalen Linie entfernt ist, der Korrosionsgewichtsverlust pro Quadratmeter 250 g beträgt. Wenn die Stahlplatte parallel zur vertikalen Linie ist, beträgt der Korrosionsgewichtsverlust 140 g pro Quadratmeter. GB/T 2423.17-1993 Standardzustände: „Die Methode zur Platzierung der flachen Probe muss so sein, dass die getestete Oberfläche in einem Winkel von 30 ° aus der vertikalen Richtung liegt.“
04 ph
Sensen Sie den pH -Wert, desto höher die Konzentration von Wasserstoffionen in der Lösung, desto sauer und korrosiver. Der pH -Wert des neutralen Salzspray -Tests (NSS) beträgt 6,5 ~ 7,2. Aufgrund des Einflusses von Umweltfaktoren ändert sich der pH -Wert der Salzlösung. Um die Reproduzierbarkeit von Salzspray -Testergebnissen zu verbessern, wird der pH -Wert der Salzlösung im Standard des Salzspray -Tests im In- und Ausland angegeben, und die Methode zur Stabilisierung des pH -Werts der Salzlösung während des Tests wird vorgeschlagen.
05
Die Menge an Salzspray -Ablagerung und Sprühmethode
Je feiner die Salzspraypartikel, desto größer die Oberfläche, die sie bilden, desto mehr Sauerstoff adsorbieren sie und desto korrosiver sind sie. Die offensichtlichsten Nachteile der traditionellen Sprühmethoden, einschließlich der pneumatischen Sprühmethode und der Sprühturmmethode, sind die schlechte Gleichmäßigkeit der Salzspray -Ablagerung und der große Durchmesser der Salzspraypartikel. Verschiedene Sprühmethoden wirken sich auch auf den pH -Wert der Salzlösung aus.
Standards im Zusammenhang mit Salzspray -Tests.
Wie lange dauert eine Stunde Salzspray in der natürlichen Umgebung?
Der Salzspray -Test ist in zwei Kategorien unterteilt, einer ist der natürliche Umwelt -Expositionstest, der andere ist der künstliche beschleunigte simulierte Salzspray -Umwelttest.
Die künstliche Simulation des Salzspray -Umwelttests besteht darin, eine Testausrüstung mit einem bestimmten Volumenraum zu verwenden - Salzspray -Testkammer in seinem Volumenraum mit künstlichen Methoden, um die Salzspray -Umgebung zu schaffen, um die Korrosionsbeständigkeit des Produkts zu bewerten. Im Vergleich zur natürlichen Umgebung kann die Salzkonzentration von Chlorid in der Salzspray -Umgebung mehrmals oder Dutzende von Zeiten des Salzspray -Gehalts in der allgemeinen natürlichen Umgebung sein Das Produkt ist stark verkürzt. Beispielsweise kann es 1 Jahr dauern, bis eine Produktprobe unter natürlicher Exposition korrodiert wird, während ähnliche Ergebnisse in 24 Stunden unter künstlich simuliertem Salzspray -Umfeld erzielt werden können.
Der künstliche simulierte Salzspray -Test umfasst einen neutralen Salzspray -Test, Acetatspray -Test, Kupfersalzbeschleunigungs -Acetatspray -Test, abwechselnden Salzspray -Test.
(1) Der neutrale Salzspray -Test (NSS -Test) ist eine beschleunigte Korrosionstestmethode mit dem frühesten Erscheinungsbild und dem breitesten Anwendungsfeld. Es verwendet eine 5% ige Natriumchlorid -Sole -Lösung, wobei der pH -Wert der Lösung im neutralen Bereich (6 ~ 7) als Sprühlösung eingestellt wurde. Die Testtemperatur wurde auf 35 ° C eingestellt, und die Siedlungsrate von Salzspray musste zwischen 1 ~ 2 ml/80 cm² liegen.
(2) Acetatspray -Test (ASS -Test) wird auf der Grundlage des neutralen Salzspray -Tests entwickelt. Es soll 5% Natriumchloridlösung etwas Gletscher Essigsäure hinzufügen, so dass der pH -Wert der Lösung auf etwa 3 fällt, die Lösung saur und schließlich das Salzspray aus neutralem Salzspray in Säure gebildet wird. Die Korrosionsrate ist etwa dreimal schneller als der NSS -Test.
(3) Kupfersalzbeschleunigter Acetatspray -Test (Cass -Test) ist ein kürzlich im Ausland entwickeltes Schnellsalz -Spray -Korrosionstest. Die Testtemperatur beträgt 50 ° und eine kleine Menge Kupfersalz - Kupferchlorid wird in die Salzlösung gegeben, um korrosion stark zu induzieren. Es korrodiert ungefähr achtmal schneller als der NSS -Test.
Unter den allgemeinen Umweltbedingungen kann die folgende Zeitumwandelformel grob erwähnt werden:
Neutrales Salzspray -Test 24h natürliche Umwelt für 1 Jahr
Acetat -Nebel -Test 24H natürliche Umwelt für 3 Jahre
Kupfersalz beschleunigte Acetat -Nebel -Test 24H natürliche Umwelt für 8 Jahre
Daher glauben wir, dass die Korrosionsbeständigkeit von Fischgefäßnoten in einer solchen Umgebung nur ein Drittel der der herkömmlichen Tests betragen sollte.
Daher glauben wir, dass die Korrosionsbeständigkeit von Fischgefäßnoten in einer solchen Umgebung nur ein Drittel der der herkömmlichen Tests betragen sollte.
Deshalb benötigen wir Angelboote, um sie zu habenMetallhalogenid -Lampe Ballastund Kondensatoren im Innenbereich installiert. Der Lampenhalter der4000W Angeln an Bordsollte mit einem Material versiegelt werden, das mehr als 230 Grad Celsius standhalten kann. Um sicherzustellen, dass die Fangleuchten bei der Verwendung des Prozesses den Versiegelungseffekt nicht und in das Salzspray verlieren, was zu einer Korrosion der Lampenkappe führt, was zu einer Glühbirnen -Chip -Pause führt.
Oben, a4000W -Fischereilampe, die Thunfisch anziehtwurde für ein halbes Jahr von einem Fischerboot verwendet. Der Kapitän hielt die Lampe nicht in einer trockenen Umgebung an Land oder überprüfte die Dichtung der Lampe, da er die Insel ein Jahr lang bewachte. Als er die Lampe nach einem Jahr wieder benutzte, explodierte der Chip der Lampe
Postzeit: Mai-15-2023